Landmines, first deployed extensively during World War II, continue to pose a significant threat in numerous regions long after conflicts have ceased. It is estimated that over 110 million landmines remain buried across more than 58 war-affected areas worldwide (see map below). These concealed explosives, designed to maim or kill, can remain active for decades, severely hindering post-conflict recovery efforts. The varied sizes and compositions of landmines necessitate the use of complementary detection technologies capable of identifying diverse materials. Techniques such as ground-penetrating radar, metal detection, and magnetic sensing are commonly employed. Additionally, advancements in remote demining methods aim to mitigate the risks associated with manual detection.
This case-study explores the potential application of Nitrogen-Vacancy (NV) magnetometers for autonomous robotic proximal sensing in landmine detection.
Existing Technical Solutions
The graphic below provides an overview of various landmine detection techniques and instruments.
Among these, magnetometers stand out as effective tools for detecting disturbances in magnetic fields, as highlighted by the green boxes. The detection of landmines through magnetic field anomalies focuses on identifying ferromagnetic components by measuring deviations in the Earth’s magnetic field. When the amount of ferromagnetic material is minimal, the need for a highly sensitive magnetometer with strong background noise cancellation becomes critical for accurate detection. The accompanying graphic illustrates the positioning of NV magnetometers in comparison to other types of magnetometers commonly employed in such detection systems.
Quantum Sensing State-of-the-Art
NV magnetometers represent an emerging and promising technology in magnetic field sensing. Recent advancements have demonstrated their potential for portable, high-sensitivity applications. Notable examples include sensitivities of 7 nT/√Hz in a compact form factor, 10 nT/√Hz with an extended dynamic range, and 28.32 nT/√Hz achieved with a miniaturized sensor. Another example, an integrated and portable magnetometer, reaches a sensitivity of 344 pT/√Hz, while the field demonstration titled „On the Road with a Diamond Magnetometer“ showcases a sensitivity of 500 pT/√Hz.
Commercially, NV magnetometers are progressing rapidly, with one available sensor achieving a resolution of 20 pT/√Hz, rivaling fluxgate magnetometers, though it comes with higher size, weight, and power (SWaP) requirements6. Future developments aim to enhance both sensitivity and SWaP performance, further expanding the applicability of this technology.
Application Needs
The following landmine characteristics are highlighted to provide context when comparing imaging technologies:
Landmine Diameter (cm) | 5 – 40 |
Landmine Burial Depth (cm) | 0 – 40 |
Plastic Landmine Metal Mass (g) | 0.6 – 2800 |
Concept of Operation
The following describes a concept of operation for an autonomous robotic system designed for landmine detection. The robot, equipped with a magnetometer mounted on a robotic arm, detects disturbances in the Earth’s magnetic field as it maneuvers over the ground. The magnetometer continuously measures the local magnetic field, identifying deviations from the Earth’s natural magnetic field caused by ferromagnetic objects, such as landmines or other buried metallic materials. These anomalies are analyzed in real time, enabling the robot to determine the object’s location, depth, and shape based on the intensity and pattern of the detected magnetic disturbances.
The proximity of the robot to the ground relaxes the sensitivity requirements for detection compared to UAV-based systems. As illustrated in the next figure, a sensitivity on the order of tens of µT is sufficient to detect an M15 landmine. Higher sensitivity becomes critical when detecting low-metal landmines or for depth and shape analysis, both essential for distinguishing landmines from other metallic objects.
For detecting small amounts of ferromagnetic material, high-sensitivity magnetometers are required. While UAV-based systems need sub-picoTesla resolution to detect steel amounts below 10g, ground-based robots can detect as little as 1g at depths up to 30 cm. At such high sensitivities, suppressing environmental noise becomes critical. A gradiometer configuration, utilizing two closely spaced magnetometers, enables common-mode noise rejection.
Depth determination is achieved by analyzing the width of the magnetic signature, which is dominated by a dipole field. The size of the signature correlates with the distance to the magnetic source. Shape characterization, meanwhile, requires resolving quadrupole and higher-order multipole fields1. These fields, which describe deviations from a perfect dipole, decay rapidly with distance, making close proximity advantageous. With sufficient sensitivity, a gradiometer measurement along the dipole axis can decompose multipole fields, allowing the reconstruction of the object’s shape.
Recommendation
To enhance landmine detection and characterization, it is recommended to begin with the development of a system based on fluxgate magnetometers integrated into a gradiometer configuration. This approach should prioritize the optimization of noise compensation, precise gradiometer positioning, and robust data processing techniques to identify object depth and shape accurately. Simultaneously, operational protocols for robotic platforms must be refined to ensure safe navigation and stable scanning without triggering landmines.
As NV magnetometers continue to improve in Size, Weight, and Power (SWaP) performance, transitioning to their use should be considered to leverage their higher sensitivity. Complementary detection systems, such as Ground Penetrating Radar (GPR) and electromagnetic induction (EMI), should also be integrated to address the limitations of magnetic detection, particularly for low-metal or plastic landmines. This phased approach will ensure a robust and versatile solution for landmine detection in diverse field conditions.
PilQrim Consulting Team
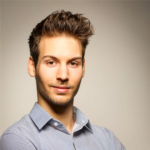
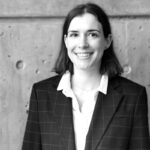
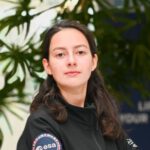